Scansonic showcases new welding optics for hairpins in electric motors
24. Jun 2019
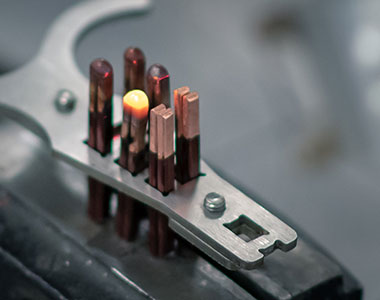
A growing number of manufacturers are using copper hairpins instead of copper winding in the production of stators. The heads of these hairpin-shaped parts are inserted into the stator and welded together by a laser beam. Each stator has 160 to 220 hairpins that are processed in a time window ranging from 60 to maximum 120 seconds. This technology reduces the overall size of electric motors and improves performance.
The biggest challenge thus far has been to reliably detect the position of the hairpins. This is because mechanical preprocessing of the hairpin surface results in different levels of reflectivity, which makes image processing more complicated. The laser welding process is extremely demanding because copper has very low absorption at room temperature. During the welding process, absorption and temperature increase sharply along with the high thermal conductivity and low molten bath viscosity of the material.
RLW-S improves performance and process reliability
Scansonic is the global market leader in laser-based joining systems for body construction. The company’s optics, sensors and process-monitoring systems are primarily used in the automotive industry, rail vehicle construction, and energy technologies. New Scansonic developments include the innovative RLW-S laser optics that are already being successfully used in production by well-known automotive suppliers.
RLW-S offers a number of key advantages. The system uses laser scanners to precisely guide the laser beam to within a tenth of a millimeter. This is made possible by an integrated camera that accurately detects the processing point and enables the welding to be completed according to a predetermined pattern. The camera also ensures continuous process monitoring and high process reliability. This gives customers maximum dependability with strong, pore-free seams at high reproduction rates. Existing laser beam sources can be fully integrated into the processing strategy.
Scansonic engineers work in close cooperation with customers on each new development. At the trade show they will be showcasing the new RLW-S along with other laser welding and brazing optics, process monitoring solutions, and sensors – including the ALO4, the next-generation, industry-leading ALO processing optics for tactile seam tracking in body construction.
2680 characters (with spaces)
About Scansonic MI GmbH
Scansonic supplies systems and solutions for laser welding, laser brazing, and laser hardening along with high-precision sensors for process monitoring. The company’s products are primarily used in the automotive industry, rail vehicle construction, and energy technologies. Scansonic MI is the global market leader in laser-based joining systems for body construction. The company is part of the Berlin.Industrial.Group. (B.I.G.). This medium-sized enterprise headquartered in Berlin has roughly 320 employees and generates annual sales of approx. €49.5 million (forecast 2019).
www.scansonic.de
Press contact
Christiane Herzer | Press and Public Relations | Berlin.Industrial.Group.
T: +49 30 912 074-566 | christiane.herzer@berlin.industrial.group
Company contact
Scansonic MI GmbH l Tel. +49 30 912 074-360 l info@scansonic.de l www.scansonic.de
Photo©: Scansonic