Scansonic presents its optics for laser welding of battery boxes in electric cars
05. Apr 2022
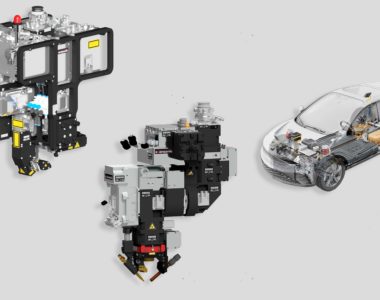
The manufacture of battery boxes presents a number of significant demands for welding technology: The weld seams must be gas-tight. The geometry is elaborate. Depending upon the aluminum alloy, there is susceptibility to cracking. Warping must be avoided. As production quantities increase, the required cycle times are now also an area of focus. Laser welding is the preferred production method, particularly because of lower energy input in the part and greater speed. Scansonic has created various solutions for these applications and offers the appropriate optics.
RLW-A remote welding optic for the underside
The fillet seams on the underside of the battery boxes can be reliably produced using remote laser welding. This method offers particular advantages based upon its high speeds and lower costs. The RLW-A remote welding optic from Scansonic is distinguished by robust system engineering, easy parameterization, and stable optical seam tracking. The optic also has two separate 2D scanners for positioning and oscillation. These allow the optic to influence melting by beam oscillation, without disturbing the seam tracking itself. With its three lines instead of the usual single line, the laser line scanner supplies more information on the position of the weld seam. Together, this ensures perfect weld seams and a high level of process safety. Laser power levels of up to 8 kW and welding speeds between 6 and 10 meters per minute are possible.
Tactile laser welding with filler wire for internal stiffness
The weld seams on the inner side of the battery boxes that are created when inserting crash structures, for example, can be optimally produced through tactile laser welding and the use of filler wire. Here Scansonic offers an appropriate solution with its ALO4 optic. Joint tracking is achieved mechanically by means of a wire introduced into the weld seam. The ALO4 produces automated, repeatable welding results to meet the high demands for fitting accuracy requirements of the battery box. In addition, the supplied filler wire – such as 4000 series aluminum wire for 6000 series aluminum sheets – significantly reduces susceptibility to cracking in aluminum alloys and ensures greater strength. The precise energy input minimizes heating of the part and prevents warping. For welding operations with particularly demanding geometric configurations, Scansonic offers the ALO4-Long version, which can create a weld seam even in cramped conditions within the battery box.
New: Combination of tactile seam tracking and laser beam oscillation
One new product in the portfolio is the ALO4-O, which was specially developed for use on battery boxes. The laser processing head combines the tactile seam tracking of the ALO product family with the laser beam oscillation of the remote optics. In this way, the ALO4-O enables a broad connection cross-section in the seam with minimal heat input, while simultaneously improving seam characteristics with the incorporated filler wire.
Development partner for new applications
In its work on the demanding welding application for battery boxes, Scansonic has been able to build on more than 20 years of process know-how in laser welding. The company’s own Laser Application Center is one of the best equipped centers of its kind in the world. Here Scansonic thoroughly tests all of its processes and develops customer-specific solutions that can function reliably in serial production. The RLW-A and ALO4 optics are based upon common system engineering in areas such as media supply, user interface, operation, and parameterization.