Scansonic at LASER World of PHOTONICS: 25 Years of Excellence in Laser-Based Metal Processing
01. Apr 2025
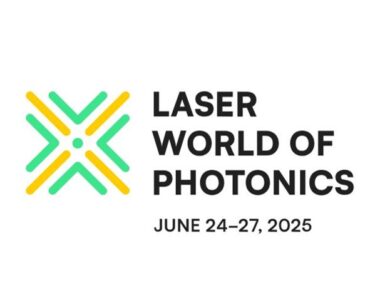
Berlin, 1 April 2025 – Celebrating 25 years of expertise in laser-based metalworking, Scansonic is presenting its expanded portfolio at LASER World of PHOTONICS 2025. Among the company’s most advanced solutions is the ALO product family, designed for laser brazing and laser welding with filler wire and tactile seam tracking.
In response to the growing demands of e-mobility, Scansonic has extended its industry-leading ALO4 system, widely used in body-in-white applications, with several new variants. The ALO4-O features beam oscillation technology, allowing for wider joint cross-sections and improved seam strength. The ALO4-L, equipped with a longer telescopic arm, is specifically engineered for deep and hard-to-reach weld seams. Making its debut in Munich is the ALO4-F, designed for particularly confined areas such as corner joints in battery housings. With these additions, Scansonic now covers all essential joining processes required for modern battery housing production. In cooperation with partners Dinse for wire feed systems and Brightlight Laser Systems for fibre lasers, customers can obtain complete and integrated system solutions from a single source.
Also on display at the Scansonic booth is a high-performance battery welding system developed by Bergmann & Steffen. This turnkey solution for laser welding cylindrical cells combines advanced image processing and fast clamping technology with Scansonic’s latest FCW system. The FCW platform stands out with its scalable number of laser spots, adaptable power output, and powerful scanners, making it ideally suited for high-volume manufacturing processes with stringent quality requirements. Typical applications include battery cells, bipolar plates, cold plates, and copper hairpins for electric motors.
Beyond these core highlights, Scansonic will also present its latest optics for laser cutting and laser cladding. These systems deliver high precision and flexibility across a wide range of metal processing tasks. The portfolio is further complemented by optical seam tracking sensors for automated arc welding, enabling accurate and efficient robotic manufacturing processes.