Battery Show Europe, Stuttgart: manufacturing solutions for the battery and e-mobility industry
21. Jun 2024
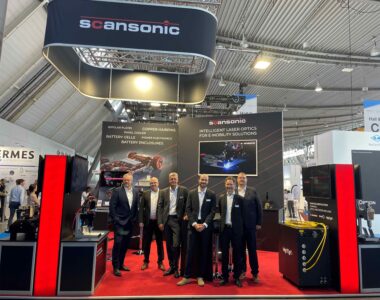
Uncompromising stability is critical
The laser processing optics on display include the ALO4 product family for laser brazing and laser welding. This family of products is particularly well-suited for laser welding of battery boxes. The production of battery boxes presents a number of significant demands for welding technology: the weld seams must be gas-tight; the geometry is elaborate; depending upon the aluminum alloy, parts may be susceptible to cracking; and warping must be avoided.
Scansonic will be exhibiting the various versions of the ALO4 – for hard-to-reach geometries within the battery box and with additional oscillation of the laser beam to increase the connection cross-section. The SCeye process monitoring system uses artificial intelligence to achieve a whole new level of quality control.
Greater output with FCW system technology
Scansonic will also be presenting its new system solution: FCW (Fast Component Welding) system technology. By arranging a number of extremely compact scanner units on a single process-specific application plate, multiple parts can be processed simultaneously to achieve higher output within the same time. Alternatively, the system’s extended scan field allows even larger components to be processed in a single step. Here, the scanner units can be individually controlled and work cooperatively. The system is also recommended for applications involving long seams or a large number of individual welds, e.g., for battery cells and contacts, bipolar plates, surface coolers, battery trays, and even hairpins for electric motors.
Expert partner for development
With low thermal energy input into the workpiece and high speeds, laser welding is ideal for the production of critical parts in electric vehicles. For these demanding welding tasks, Scansonic can draw on more than 25 years of process know-how in laser welding. The company’s own Laser Application Center is one of the best equipped centers of its kind in the world. In the center’s eleven laboratories, Scansonic works together with its customers to exhaustively test all processes, geometries, and materials, and to deliver individual solutions that produce reliable results in serial production.