Fast and robust sheet metal laser welding
25. Oct 2022
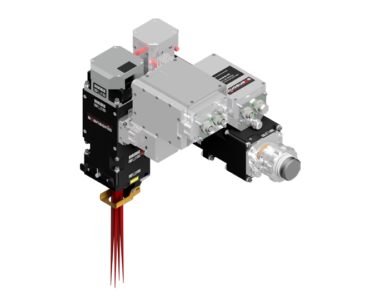
Scansonic is one of the world’s top companies for laser welding, brazing, cutting, hardening, and surface coating, offering a wide range of optics for various applications. With its many proven components and technologies, Scansonic can offer the right optic for any use, from simple to highly complex.
The LPH-O series uses Scansonic’s modular scapacs® system. This system uses additional integrated scanners to move the welding point on the part surface with a frequency of up to 700 Hz. In the process, the focus oscillates by several millimeters in a circular or spiral shape along the weld seam, for example, while the guide machine, usually a robot, moves the optic. This increases the weld seam width while using a comparatively small spot. The result is greater gap bridging with low heat input, as well as a more robust process and an increase in maximum process speed.
LPH-O optics are used in applications such as the production of prismatic battery cells. Here, extremely thin aluminum covers (approx. 1 mm) are welded onto the battery’s aluminum housing. Sealed seams and the highest possible welding speed are the main priorities for this application. Because of the battery’s very thin walls, heat input is a critical parameter. The use of the LPH-O and an oscillating laser beam increased the welding speed by 30%. It also produced a significantly smoother seam surface. The optic was supplemented with a specially developed shielding gas nozzle for this aluminum-related application.
Additional functions can also be added to the LPH-O series optics when required for specific customers or applications.
When welding Tailored Welded Blanks (TWB) for hot forming, for example, an LPH-O optic is equipped with a telescoping arm to supply filler wire and an associated autofocus function to control the operation. TWB boards are formed after welding, which places the highest demands on weld seam quality. This applies in particular to boards used for hot forming. The metal plates have an AlSi coating and this creates the risk of intrametallic phase formation, which could lead to cracks during deep drawing. The weld areas are therefore generally laser decoated beforehand.
The LPH-O with filler wire allows the targeted use of oscillation and filler wire to influence the process and prevent the creation of intermetallic phases in the critical areas. This eliminates the need for laser decoating.
In addition to the shielding gas nozzle, filler wire, and autofocus, protective glass monitoring can also be added to the LPH-O. Scansonic optics also allow the integration of “SCeye,” a camera-based quality monitoring system. If seam tracking or image recognition options are needed in addition to these other options, customers can select remote optics from the RLW family or tactile optics from the ALO family.
Testing customer-specific applications in the Laser Application Center
For all of its optics, Scansonic focuses on providing the optimal type for each customer application. This customer-centric approach is made possible by Scansonic’s modular system, which allows the company to offer its optics with the necessary features for every application. The Laser Application Center in Berlin has ten fully equipped laser laboratories, making it one of the largest such centers in the world. Customer applications can be thoroughly tested here to optimize process parameters and select the right optic.
More information on Scansonic laser welding optics can be found at: https://www.scansonic.de/en/applications/laser-welding/